Full Version: Vector Cutting Method
From: JHayes55 [#4]
10 Mar 2007
To: Engravin' Dave (DATAKES) [#1] 10 Mar 2007
EDITED: 10 Mar 2007 by JHAYES55
From: Engravin' Dave (DATAKES) [#5]
10 Mar 2007
To: ALL
Thanks for all of your responses. I was hoping to learn how much of an impact the misting had in actually lessening the heat buildup on the under side of the plastic.
I don't do a great deal of vector cutting, but the other day I stepped a little outside of my comfort zone with my creative thoughts and came up with a plaque design for a customer that uses their 3-color logo as the plaque plate that would ultimately contain some engraved text.
Since the logo would be cut out of three different colors of material, then put together like a puzzle, I wanted the cutting tolerances to be pretty precise, hopefully producing a clean look at the seems with no noticable gaps.
Well, I did my cutting today, will raster the text and adhere to the plaque boards Monday.
I hope my customer is as thrilled with the results as I am. I was a little nervous over this one, but my equipment came through with flying colors.
I'll post a picture of the finished product on Monday.
From: Mike (MIKEN) [#6]
10 Mar 2007
To: Engravin' Dave (DATAKES) [#5] 11 Mar 2007
Dave:
For most of my cutting applications the Rowmark suggestion isn't the answer. I'm doing name tags and office name plates which obviously must be engraved and cut face up on the laser in the same operation.
IF it's a straight vector cut then I agree that cutting from the back is better, but on a grid and all the way through. The trick is not to overpower the cut and to mask it.
When doing inlays cutting from the back is the preferred method as you can reduce the laser kerf and get a better fit.
Herre's a picture (not good) of an abalone inlay I just finished. The abalone was cut from the back in numerous passes.
EDITED: 10 Apr 2007 by MIKEN
From: JHayes55 [#7]
10 Mar 2007
To: Mike (MIKEN) [#6] 10 Mar 2007
How thick was the abalone?
From: Mike (MIKEN) [#8]
10 Mar 2007
To: JHayes55 [#7] 11 Mar 2007
It was .050" and I cut it in several passes because I was afraid I would fracture it. It is very delicate and has many varying densities.
I applied glue to the rastered part and pressed the abalone into place with a piece of hardwood and light taps with a hammer. Then sanded it smooth.
Enough to do four names is about $50.
From: Doc (GREAT_ATLANTIC) [#9]
11 Mar 2007
To: Engravin' Dave (DATAKES) [#5] 11 Mar 2007
Dave...
When cutting the inside pieces of the plastic, how did you account for the kerf of the laser cut....do you make those pieces slightly larger? Ive not done any inlay, but it's one of those things on the list I'd like to try (...the same for wood intarsia.) Does this technique improve the cut?
From: Stunt Engraver (DGL) [#10]
11 Mar 2007
To: Mike (MIKEN) [#8] 11 Mar 2007
There is, or used to be, thin sheets of abalone (abalone-like?) made specifically for laser inlay.
The material also came in other colors and patterns.
From: Stunt Engraver (DGL) [#11]
11 Mar 2007
To: ALL
Here's a post where Mike Mackenzie elaborates on the inlay process and in an ensuing post, the abalone (Ablam) material I spoke of:
http://engravingetc.org/forum/index.php?webtag=EE&msg=647.9
EDITED: 11 Mar 2007 by DGL
From: Mike (MIKEN) [#12]
11 Mar 2007
To: Doc (GREAT_ATLANTIC) [#11] 11 Mar 2007
The abalone is a natural shell material with varying degrees of density. I enlarged my drawing by .005" to allow for the kerf and was able to do the first piece but on the second I only enlarged the drawing by .002".
If I were inlaying plastic or wood where I cut through the material I would go back to the .005".
David:
My customer provided the material and requested that I use it as opposed to the thinner ablam.
I used blue painters tape on the underside to keep the material together.
I concur with the remarks by Mike Mackenzie.
From: Stunt Engraver (DGL) [#13]
11 Mar 2007
To: Mike (MIKEN) [#12] 12 Mar 2007
The customer's always right!
I've always been fascinated by inlay work. It would be one of the reasons I'd buy a laser.
From: Doc (GREAT_ATLANTIC) [#14]
11 Mar 2007
To: Mike (MIKEN) [#12] 12 Mar 2007
From: Engravin' Dave (DATAKES) [#15]
12 Mar 2007
To: ALL
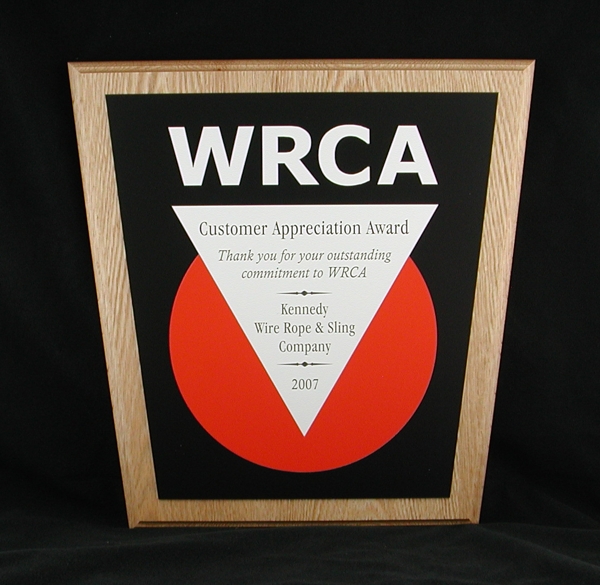
EDITED: 12 Mar 2007 by DGL
From: Doc (GREAT_ATLANTIC) [#16]
12 Mar 2007
To: Engravin' Dave (DATAKES) [#15] 12 Mar 2007
From: Engravin' Dave (DATAKES) [#17]
12 Mar 2007
To: Doc (GREAT_ATLANTIC) [#16] 12 Mar 2007
Jim,
Thank you.
I did a test run on a small piece of the same material which resulted in such a nice snug fit, I decided to run without an adjustment. I used Rowmark's LaserMax material from Johnson Plastics.
Mike offered very sound advice. The figure will likely need to be adjusted based on your machine, as well as the material you are cutting, be it wood, plastic, acrylic, etc.
EDITED: 12 Mar 2007 by DATAKES
From: Stunt Engraver (DGL) [#18]
12 Mar 2007
To: Engravin' Dave (DATAKES) [#15] 12 Mar 2007
Did you use typical engraving stock for the three colors?
From: Engravin' Dave (DATAKES) [#19]
12 Mar 2007
To: Stunt Engraver (DGL) [#18] 12 Mar 2007
From: Stunt Engraver (DGL) [#20]
12 Mar 2007
To: Engravin' Dave (DATAKES) [#19] 12 Mar 2007
I'm glad you explained the plaque was intentionally shaped as a trapezoid.
I thought it was a weird camera angle. :-)
Message 6287.21 was deleted
From: Stunt Engraver (DGL) [#22]
12 Mar 2007
To: Engravin' Dave (DATAKES) [#21] 12 Mar 2007
So far, Chroma-Crystal would fall under digital imaging. If the subject became rampant, we could create a specific folder.
From: Mike (MIKEN) [#23]
12 Mar 2007
To: Engravin' Dave (DATAKES) [#20] 12 Mar 2007
Great work and a kind we don't see enough of.